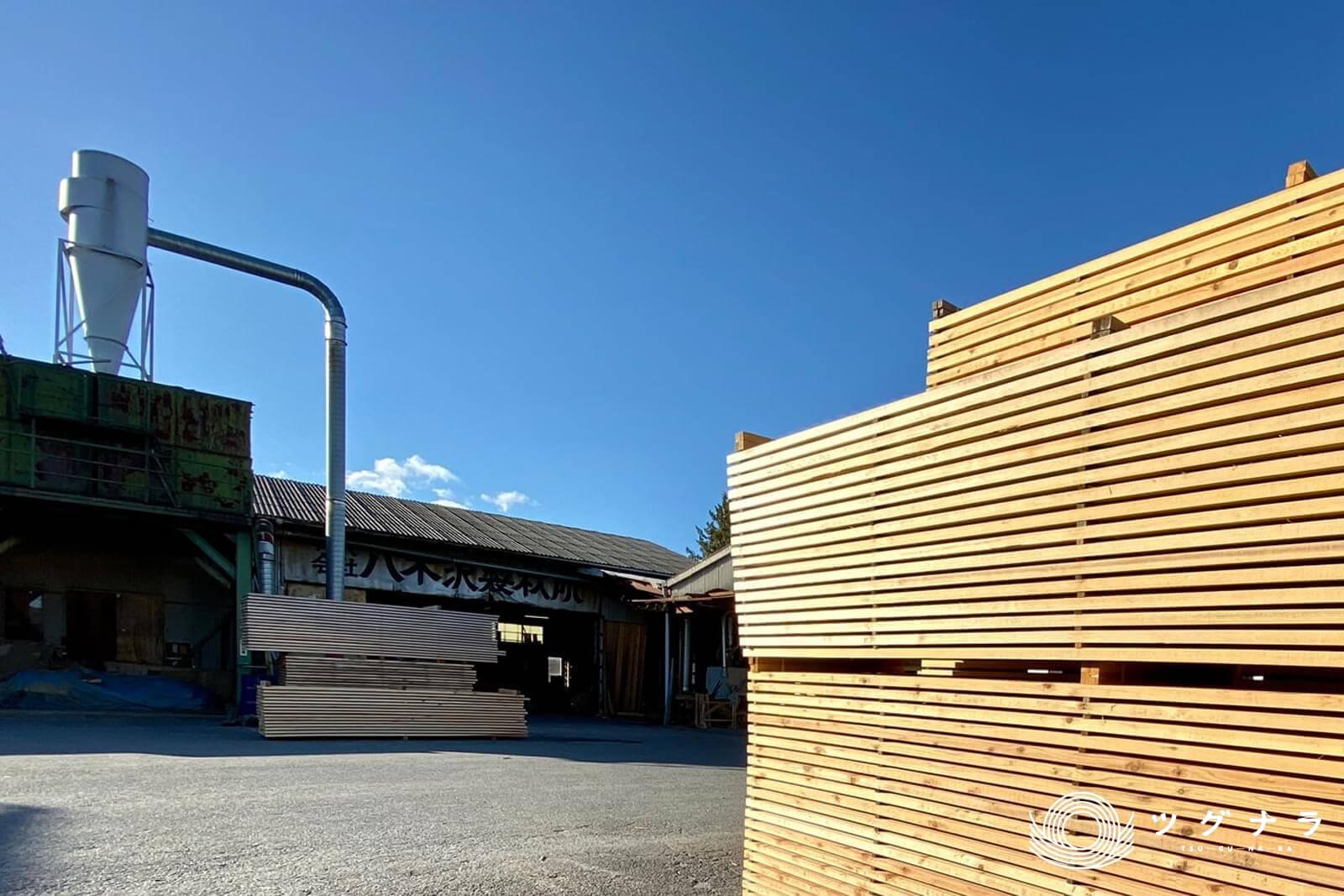
日光
日光市
長年にわたり地元の日光市産の木材を中心に製材・販売をおこなう
株式会社ヤギサワ
独自の加工木材・不燃木材で市場開拓しながら成長する木材のクリエイター
経営理念
森林資源を活用する木材生産を通して地域資源と社会を繋ぐ架け橋となり、資源、空間、環境に寄与することで人が働く価値を創造する
高品質の製品を提供します
弊社は、木材の製材・加工・販売を主力業務とする企業で、長年にわたり日光市産の木材を中心に製材・販売を行ってきました。
現在は、一般の製材業はもとより、硬質木材(杉光WAVES)、熱処理木材(SOTOMO)など独自の特殊木材の製造も行っております。
また、2016年には近年の木造・木質化の建築ニーズ増大に対応した不燃・準不燃木材の製造を開始し、CoC森林認証材の製品の提供も可能となりました。
私たちは、これからも日光市産・栃木県産の木材を中心に時代のニーズに対応した製品、価値のある製品を提供し続けていきたいと思っております。
代表者メッセージ
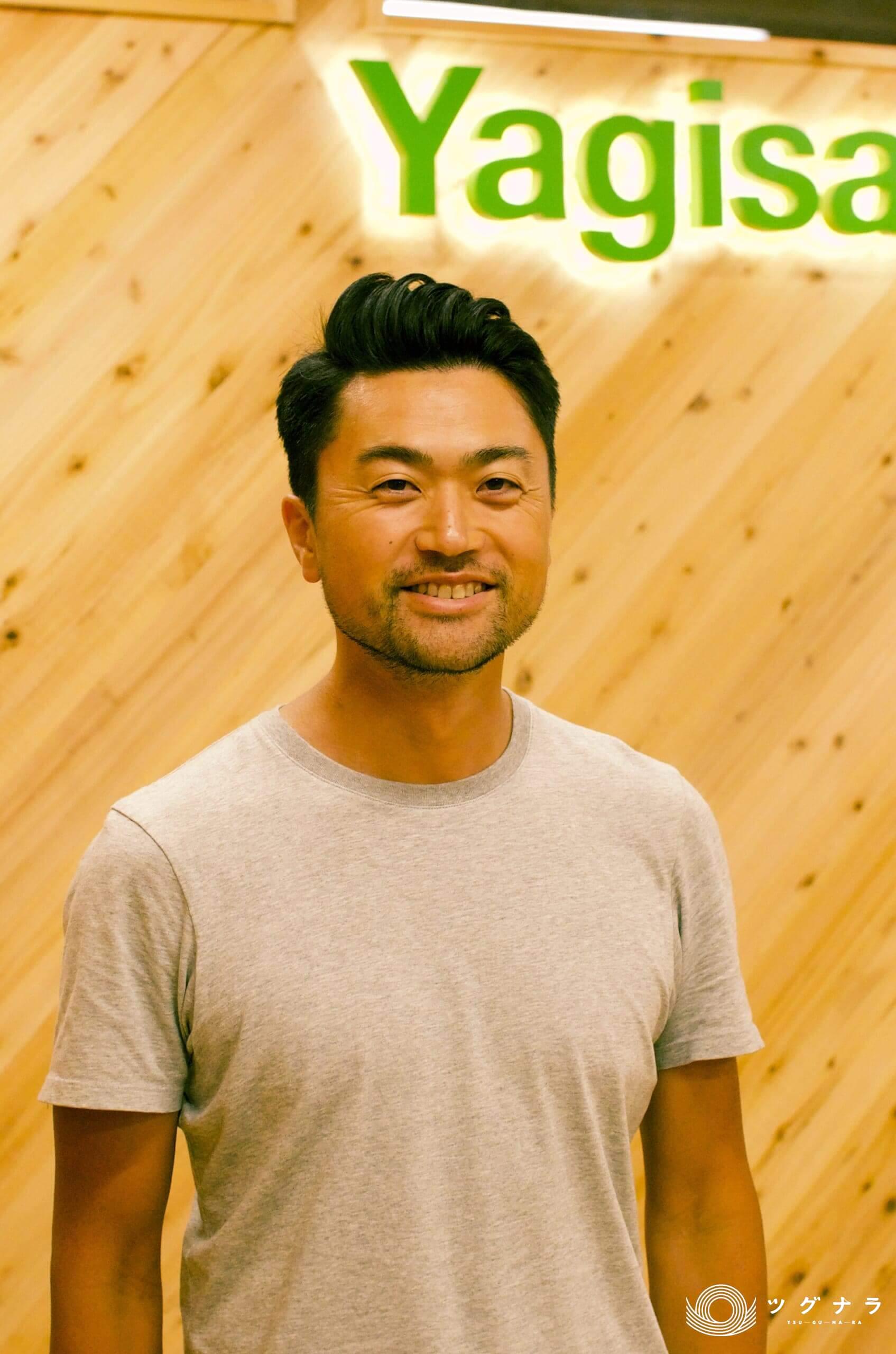
事業承継はいつおこなわれましたか
今、私は38歳になりますが2021年9月に先代から事業を引き継ぎます。事業承継をしたと言いましたが、正直なところ、普段の業務では特段に変わっていません。本当に役職名だけが変わっただけ、という感じしか今はありません。
新型コロナウィルスの件もあり社会全体からみれば、先行き不安な時代ではありますが、あまり不安は感じておりません。理由としては、ここ十数年間で今の木材関連の業界で取り組めることに対し、準備をしてきているからです。また、日本の住宅で使用している木材の大半が輸入に頼っている現状で、新型コロナウィルスの影響で起こっているウッドショック(短期間で急激に木材が不足し価格の高騰が起きること)で需給のバランスが崩れ、価格の高騰に歯止めがかからない状態になっていますが、弊社で製造している不燃木材は影響が少なく需要も高いため、注文もいただいており経営状態としては悪くない状態です。
事業承継を意識したタイミングと従事したきっかけは
大学卒業後、すぐに入社したので、今年で入社してから16年目になります。勤続年数が私より長い社員は2名いるのでお目付け役のようでバランスが取れています。大学の専攻も家業を意識して決めており物心ついたときから意識はしていました。大学生の時に、スケートボードとスノーボードにはまっていたことは楽しい思い出です。大学生活ではいい出会いも多くあり、勉強よりも、友人や先輩と過ごした時間が思い出になっています。大学で専攻していた学部は、生物資源学部の森林資源学科です。森林資源科学科でしたが、同じクラスメートで木材であったり林業関係の事業承継者や勤めたいと思う人は少なかったのを記憶しています。しっかりと勉強している人たちの中には、就職先に県庁、市役所といった公務員を選び、試験に受かっている人もいました。私は勉強に関しては不真面目でしたが、学部学科の中では学んだことを活かした仕事に就いていることは自負できます。家業へ入社した直後は、気持ちの部分で切り替えが出来なかった部分があります。そのため、就業時間内に仕事はきっちりと終わらせて、趣味のスケートボードへ行く日々でした。いつも暗くなるまで打ち込んでいましたが、家業も手を抜いていたわけではありません。作業は好きでしたし、配達の業務もやたっりと、うまく両立できていたと思います。
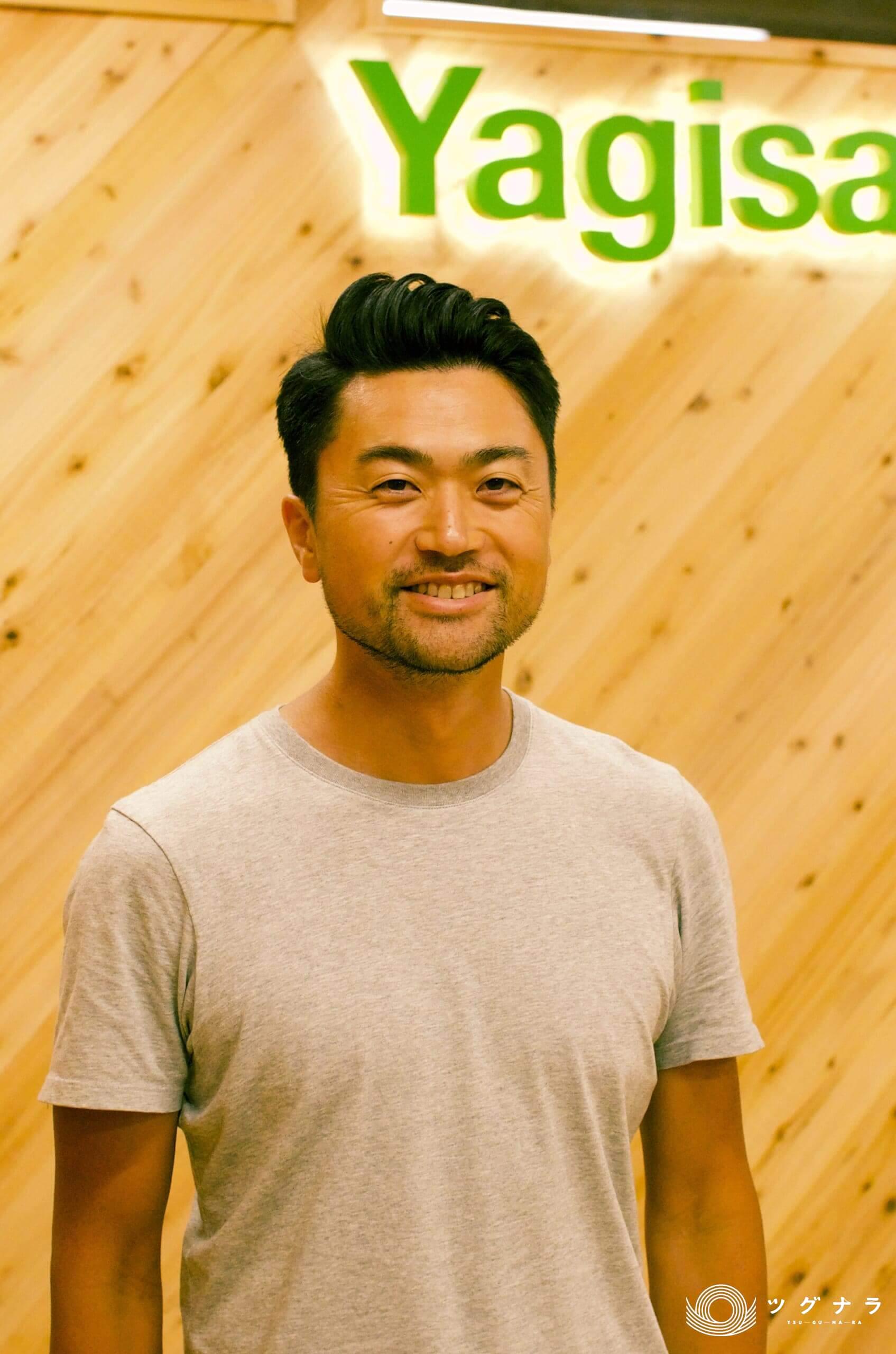
私たちのこだわり
特殊木材で最初に作ったものとは
最初に作った特殊なものは、2011年に引き受けた企画で圧密化木材(木材の強度を上げるために、加熱、加圧して圧密化する圧密化処理を木材に施したもの)の開発は、先代の社長のつてで紹介してもらい、始めました。最初は丸太を転がすように圧縮するような要望でしたが、現実として機械で加工は難しいと判断し、空気圧縮を試したりもしました。今思えば、不確定要素が多く先行した設備投資になってしまったと思います。そこが自社にとって商品開発をおこなう良いきっかけとなりました。機械を導入してからは、原料(素材)の投入量から期待される生産量に対して、実際に得られた製品生産数(量)比率でもある歩留まりが悪く、思ったようなモノはできませんでした。
この時に発案者でもある宮城県の開発者と一緒に仕事をする機会により、開発者に触れたことが後の商品開発を加速し自分自身でもものづくりを強く意識するようになりました。
乾燥材の分野での開発秘話
先代の社長の時代に、ちょうど乾燥材(寸法変化のほとんどない優れた建築材料)が普及してきたのですが、弊社ではその流れに乗ることが出来ませんでした。乾燥材とともにプレーナー(表面がざらついた状態の木材を、表面を平滑に整えた状態にすること)かける材料も少なく、仕上げ加工をする前段階の板の状態でもある荒木のままで出荷する方が多かったです。乾燥するにしても、天然乾燥とか、ちょっと木材を立てておいて時間をおく程度の乾燥でした。寸法もバラバラだったため取引先に配達へいくと、昔から顔見知りの大工さんたちからあまり良く思われませんでした。
自分自身で配達していましたので問題点を把握することができ、ご指摘を受けたことは反省しすぐに対策を考えました。
前述した特殊木材の開発も上手くいっていませんでしたが、導入していた機械にボイラーが付いていたことに着目し、それを使って乾燥機を作ってみようと思いつきました。当時は、時代のニーズにあった木材を作る基本的なプロセスが社内にはありませんでした。木材に長けていた機械メーカーの担当部長に相談して、木材の乾燥方法について学び実行しました。
木材加工で芯持ちの角材を割らずに乾燥するというのは、難易度が高いものでした。しかし、日本の技術が優れている点ではありますが、ドライニングセットという外側を高温セットし、内側をだんだん乾かしていく手法が国内の同業ではスタンダート(標準化)になっていきました。構造材というのは、量産の工場で生産した方が効率も良いのですが、価格が見合いません。一方、海外のモノは芯も含めほとんど板割に製材し、乾燥機も中温のものを使用するため難易度は高くはありません。板にしてしまえば熱と風さえがあれば、中温乾燥で乾くことも分かったので熱源をどう確保するのかを考えました。最初はボイラーの蒸気を熱源にしていましたが、ボイラーだと燃料代も掛かるため電気を熱源とするオイルヒーターを試してみました。ステンレス製のタンクを作りそこに熱源となる電熱棒を取付けました。温度が上がるとタンクの中の油が膨張してしまうのでリザーブタンクを付けて膨張槽を設けたり、試行錯誤をしました。実機を作りながらもトラブル続きで、油が減って電熱棒が漏電してしまったり、何度も失敗を繰り返しながら改良を重ね徐々にシステム化に成功し、その後、実機を計3機ほど作りました。工場見学にいらっしゃる外部の人からは乾燥機を自社開発したことを説明すると驚かれます。また、自分で作ったものなので故障しても自分で修理やメンテナンスもできることがメリットです。乾燥材への参入が遅れましたが基礎から学び自分で作ったことにより、弊社の主力商品となったことは大きかったです。2012~2013年頃の話になります。
不燃木材製造のきっかけ
このころは周りからの後押しもあり、展示会へ出店するようになりました。色々なものを見て、考える良いきっかけとなりました。展示会は参加者として見に行くのと、展示出店者としてでは意識が変わってきます。一番は2、3日常駐するので他のブースのメーカーの人や来場者の方とじっくり話す機会があるところです。その中で木材に高温の熱だけを加えて防腐防蟻機能をつける技術に直面しました。一般的に防腐剤など薬品を使うことは、好まず信用もしていませんでした。その理由として、リフォーム現場でも防腐剤を注入した外構材が腐っているのも見たことがあったからです。これを機に高温熱処理木材(SOTOMO)も開発し、製造に至りました。
またある時に、圧縮木材の販売をしていましたが設備の稼働率が悪く代わりになるものがないかと思っていたときに、不燃木材に出会いました。以前にも原板を持込み、不燃薬品を注入してもらい納品したことがありましたが、不燃木材は原価も高いものでした。普通の加工板だと1立法メートルあたり20万円ですが、不燃材になると3倍以上の70万円で売れます。自社で持っていた機械が、不燃薬品の圧力注入に使用している同じメーカーでもあったので、担当者に連絡をして不燃材の会社の方を紹介してもらい実物など見学へ行きました。色々な人との出会いで、不燃木材に挑戦しようと考え、機械を少し改造すれば不燃薬品の注入に対応できることもわかり取り掛かりました。
不燃木材の開発は、大学で学んできた知識が少し役立ちましたが、当時はあまり真剣に学んでいなかったことからも自分で興味を持たないと勉強はしないものだと痛感しました。それは裏を返せば知的好奇心なのかもしれず勉強ではなく開発に集中していました。
不燃木材のニーズと潜在価値について
最初から不燃木材の売れ行きは好調で、嬉しいことに地域での利用例が多かったことです。不燃木材の取り扱い始めた翌年には、日光市の本庁舎が建て替えということもあり、内装に使用する木材はすべて準不燃が必須でした。公共建築物を木造木質化していくという国の方針がある一方で、公共建築物は防火対策に十分配慮する必要があるため不燃木材のニーズがあると確信していきました。
以前は自社建築も行いながら、製品販売も行ってきましたが、ハウスメーカーと製材メーカーの市場で比較した場合に、製材市場の方が競合相手が圧倒的に少ないことは分かっていました。そこで製材で勝負できるようにと乾燥材を作れるように進めていきまし、製品の価値を上げるために不燃木材をやりました。これらは、最初の特殊木材による未知な設備投資が始まりでしたが、点と点が繋がっていき今ではしっかりと事業を支える面になってきました。不燃材については、首都圏、東北エリアにも納品実績が増加し、関西エリアにも少しずつ実績が増えていきそうです。業界としても私の年代では一番熟知していると思っています。昔からあった市場ではありますが良いタイミングで参入できたと思っています。
乾燥機を自社で作成するなど、チャレンジと失敗の積み重ねたことにより、不燃木材の製造方法にも探求できたことが要因になっていると思います。また、様々な専門家の方にも基本をしっかりと教わりながら、試行錯誤と独自ノウハウを身に付けていったことは大きな自信になりました。
社長の強み
好きなモノや自分がやりたいものに関しては、自分で考え没頭するタイプだと思います。そこが仕事にも生きてますし、行動に移すときは大胆に発想はするもののリスクも取れている方だと思います。
経営や経済を学んでいくことにはまだ課題はありますが、会社を大きくしていきたい、市場の発展性などに関心や興味への追求はあり、誰かれ構わずに相談し質問して実践できることは不確実性の高い現代においては、変化を恐れずに進めることは自分の強みかと思います。
それから、無理だろうなという仕事でも断らないでやってきたというのが根幹にあります。細かい仕事や、反対に量を求められる仕事も断らないでやってきました。栃木県内の製材メーカーを知っているため、材料が足りなければ分けてもらったりして対応しました。地域の人たちとは持ちつ持たれつの良い関係を築けています。

特殊木材で最初に作ったものとは
最初に作った特殊なものは、2011年に引き受けた企画で圧密化木材(木材の強度を上げるために、加熱、加圧して圧密化する圧密化処理を木材に施したもの)の開発は、先代の社長のつてで紹介してもらい、始めました。最初は丸太を転がすように圧縮するような要望でしたが、現実として機械で加工は難しいと判断し、空気圧縮を試したりもしました。今思えば、不確定要素が多く先行した設備投資になってしまったと思います。そこが自社にとって商品開発をおこなう良いきっかけとなりました。機械を導入してからは、原料(素材)の投入量から期待される生産量に対して、実際に得られた製品生産数(量)比率でもある歩留まりが悪く、思ったようなモノはできませんでした。
この時に発案者でもある宮城県の開発者と一緒に仕事をする機会により、開発者に触れたことが後の商品開発を加速し自分自身でもものづくりを強く意識するようになりました。
乾燥材の分野での開発秘話
先代の社長の時代に、ちょうど乾燥材(寸法変化のほとんどない優れた建築材料)が普及してきたのですが、弊社ではその流れに乗ることが出来ませんでした。乾燥材とともにプレーナー(表面がざらついた状態の木材を、表面を平滑に整えた状態にすること)かける材料も少なく、仕上げ加工をする前段階の板の状態でもある荒木のままで出荷する方が多かったです。乾燥するにしても、天然乾燥とか、ちょっと木材を立てておいて時間をおく程度の乾燥でした。寸法もバラバラだったため取引先に配達へいくと、昔から顔見知りの大工さんたちからあまり良く思われませんでした。
自分自身で配達していましたので問題点を把握することができ、ご指摘を受けたことは反省しすぐに対策を考えました。
前述した特殊木材の開発も上手くいっていませんでしたが、導入していた機械にボイラーが付いていたことに着目し、それを使って乾燥機を作ってみようと思いつきました。当時は、時代のニーズにあった木材を作る基本的なプロセスが社内にはありませんでした。木材に長けていた機械メーカーの担当部長に相談して、木材の乾燥方法について学び実行しました。
木材加工で芯持ちの角材を割らずに乾燥するというのは、難易度が高いものでした。しかし、日本の技術が優れている点ではありますが、ドライニングセットという外側を高温セットし、内側をだんだん乾かしていく手法が国内の同業ではスタンダート(標準化)になっていきました。構造材というのは、量産の工場で生産した方が効率も良いのですが、価格が見合いません。一方、海外のモノは芯も含めほとんど板割に製材し、乾燥機も中温のものを使用するため難易度は高くはありません。板にしてしまえば熱と風さえがあれば、中温乾燥で乾くことも分かったので熱源をどう確保するのかを考えました。最初はボイラーの蒸気を熱源にしていましたが、ボイラーだと燃料代も掛かるため電気を熱源とするオイルヒーターを試してみました。ステンレス製のタンクを作りそこに熱源となる電熱棒を取付けました。温度が上がるとタンクの中の油が膨張してしまうのでリザーブタンクを付けて膨張槽を設けたり、試行錯誤をしました。実機を作りながらもトラブル続きで、油が減って電熱棒が漏電してしまったり、何度も失敗を繰り返しながら改良を重ね徐々にシステム化に成功し、その後、実機を計3機ほど作りました。工場見学にいらっしゃる外部の人からは乾燥機を自社開発したことを説明すると驚かれます。また、自分で作ったものなので故障しても自分で修理やメンテナンスもできることがメリットです。乾燥材への参入が遅れましたが基礎から学び自分で作ったことにより、弊社の主力商品となったことは大きかったです。2012~2013年頃の話になります。
不燃木材製造のきっかけ
このころは周りからの後押しもあり、展示会へ出店するようになりました。色々なものを見て、考える良いきっかけとなりました。展示会は参加者として見に行くのと、展示出店者としてでは意識が変わってきます。一番は2、3日常駐するので他のブースのメーカーの人や来場者の方とじっくり話す機会があるところです。その中で木材に高温の熱だけを加えて防腐防蟻機能をつける技術に直面しました。一般的に防腐剤など薬品を使うことは、好まず信用もしていませんでした。その理由として、リフォーム現場でも防腐剤を注入した外構材が腐っているのも見たことがあったからです。これを機に高温熱処理木材(SOTOMO)も開発し、製造に至りました。
またある時に、圧縮木材の販売をしていましたが設備の稼働率が悪く代わりになるものがないかと思っていたときに、不燃木材に出会いました。以前にも原板を持込み、不燃薬品を注入してもらい納品したことがありましたが、不燃木材は原価も高いものでした。普通の加工板だと1立法メートルあたり20万円ですが、不燃材になると3倍以上の70万円で売れます。自社で持っていた機械が、不燃薬品の圧力注入に使用している同じメーカーでもあったので、担当者に連絡をして不燃材の会社の方を紹介してもらい実物など見学へ行きました。色々な人との出会いで、不燃木材に挑戦しようと考え、機械を少し改造すれば不燃薬品の注入に対応できることもわかり取り掛かりました。
不燃木材の開発は、大学で学んできた知識が少し役立ちましたが、当時はあまり真剣に学んでいなかったことからも自分で興味を持たないと勉強はしないものだと痛感しました。それは裏を返せば知的好奇心なのかもしれず勉強ではなく開発に集中していました。
不燃木材のニーズと潜在価値について
最初から不燃木材の売れ行きは好調で、嬉しいことに地域での利用例が多かったことです。不燃木材の取り扱い始めた翌年には、日光市の本庁舎が建て替えということもあり、内装に使用する木材はすべて準不燃が必須でした。公共建築物を木造木質化していくという国の方針がある一方で、公共建築物は防火対策に十分配慮する必要があるため不燃木材のニーズがあると確信していきました。
以前は自社建築も行いながら、製品販売も行ってきましたが、ハウスメーカーと製材メーカーの市場で比較した場合に、製材市場の方が競合相手が圧倒的に少ないことは分かっていました。そこで製材で勝負できるようにと乾燥材を作れるように進めていきまし、製品の価値を上げるために不燃木材をやりました。これらは、最初の特殊木材による未知な設備投資が始まりでしたが、点と点が繋がっていき今ではしっかりと事業を支える面になってきました。不燃材については、首都圏、東北エリアにも納品実績が増加し、関西エリアにも少しずつ実績が増えていきそうです。業界としても私の年代では一番熟知していると思っています。昔からあった市場ではありますが良いタイミングで参入できたと思っています。
乾燥機を自社で作成するなど、チャレンジと失敗の積み重ねたことにより、不燃木材の製造方法にも探求できたことが要因になっていると思います。また、様々な専門家の方にも基本をしっかりと教わりながら、試行錯誤と独自ノウハウを身に付けていったことは大きな自信になりました。
社長の強み
好きなモノや自分がやりたいものに関しては、自分で考え没頭するタイプだと思います。そこが仕事にも生きてますし、行動に移すときは大胆に発想はするもののリスクも取れている方だと思います。
経営や経済を学んでいくことにはまだ課題はありますが、会社を大きくしていきたい、市場の発展性などに関心や興味への追求はあり、誰かれ構わずに相談し質問して実践できることは不確実性の高い現代においては、変化を恐れずに進めることは自分の強みかと思います。
それから、無理だろうなという仕事でも断らないでやってきたというのが根幹にあります。細かい仕事や、反対に量を求められる仕事も断らないでやってきました。栃木県内の製材メーカーを知っているため、材料が足りなければ分けてもらったりして対応しました。地域の人たちとは持ちつ持たれつの良い関係を築けています。
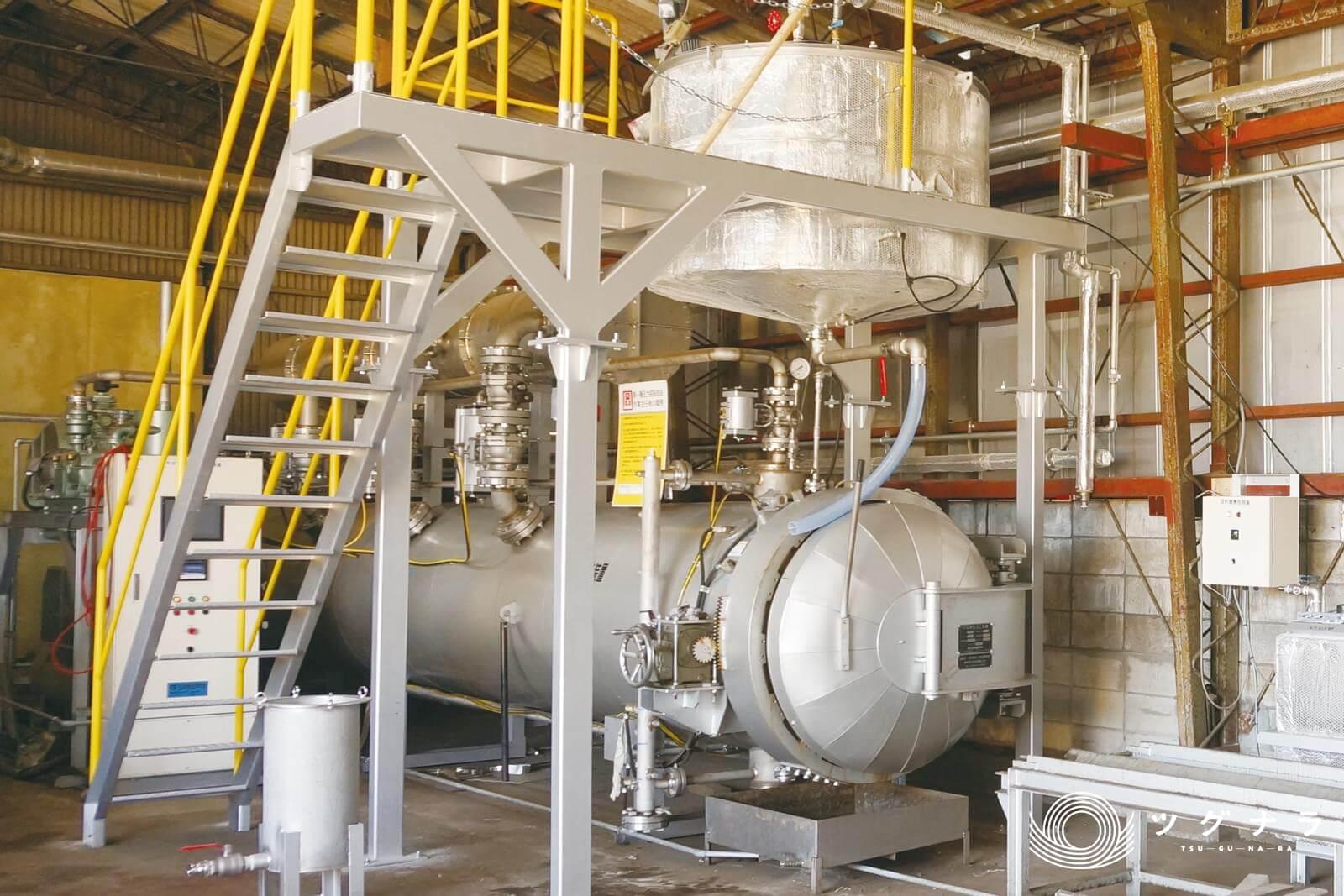
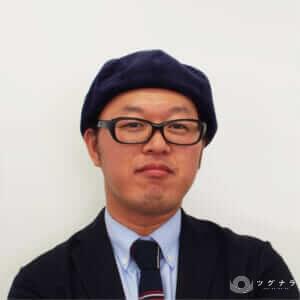
ツグナラコンサルタントによる紹介
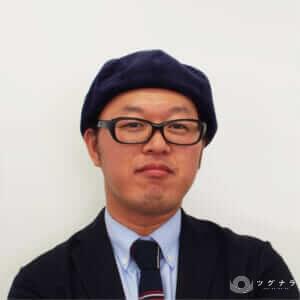
10年以上のお付き合いをさせていただいていますが、その過程でインタビューにご対応いただいた新社長のもと、さまざまな取り組みをしながら着実な成長を遂げてきました。この業界におけるオピニオンリーダーとしての活躍が今後も見続けられることを期待しております。
インタビュアーのコメント
会社概要
社名 | 株式会社ヤギサワ |
創立年 | 1927年 |
代表者名 | 代表取締役 八木澤 享一 |
資本金 | 1000万円 |
本社住所 |
321-1264 栃木県日光市瀬尾252 0288-21-0005 |
事業内容 | 製材・木材販売、建材販売 |
URL |
https://yagisawa-nikko.jp/
|
公開日:2021/07/16 (2023/01/25修正)
※本記事の内容および所属名称は2023年1月現在のものです。現在の情報とは異なる場合があります。