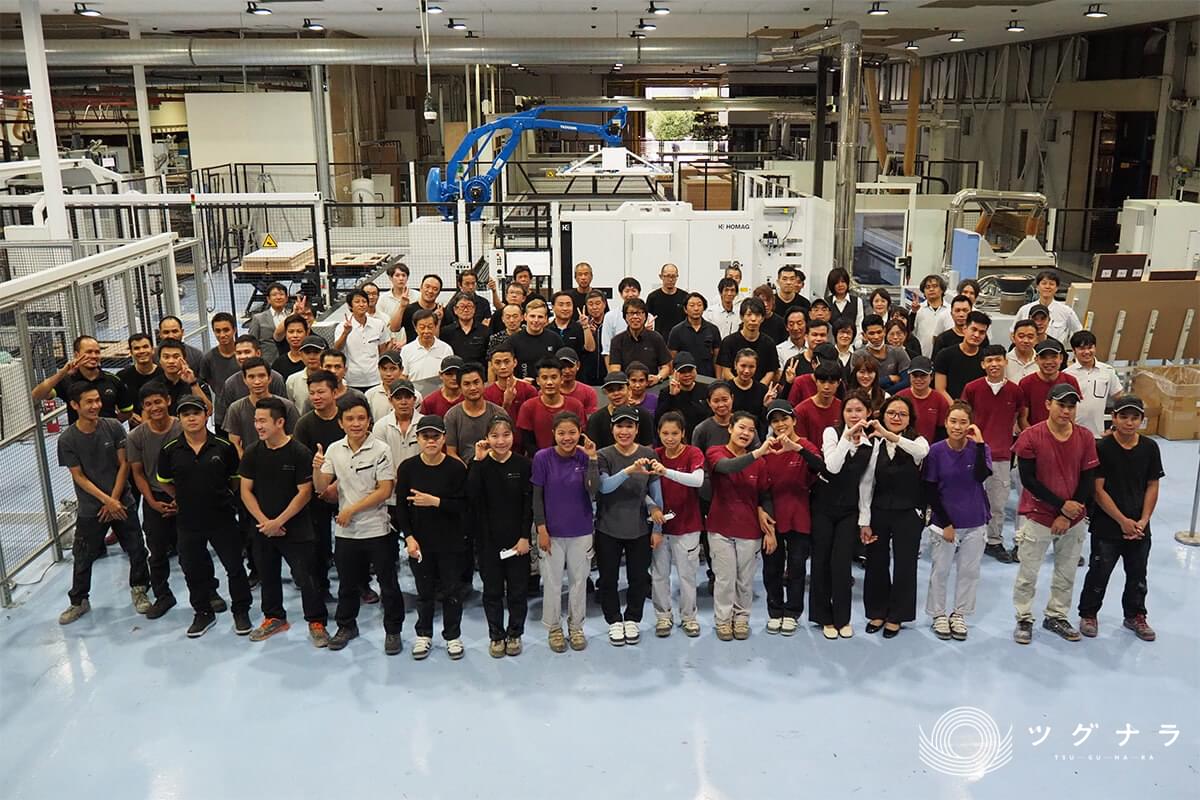
各務原
各務原市
DXで木工業界の潜在力を引き出す創業80年のスマートファクトリー
豊桑産業株式会社
挑戦と革新の融合で一歩先の未来を刻む「人」とデジタルの共存
経営理念
一歩先行く木工会社
豊桑産業は長年、建材製造・建材加工をベースに企業技術を強化し続け、さらなる技術向上を目指した会社づくりに取り組んできました。「人」を大切にし、創造性豊かな人材を育成することで現場の向上に努めています。
加工から組立まで一貫生産する現場力で生産効率を上げ、コスト低減を実現できる環境を整え、業界をリードする企業として進み続けます。
代表者メッセージ
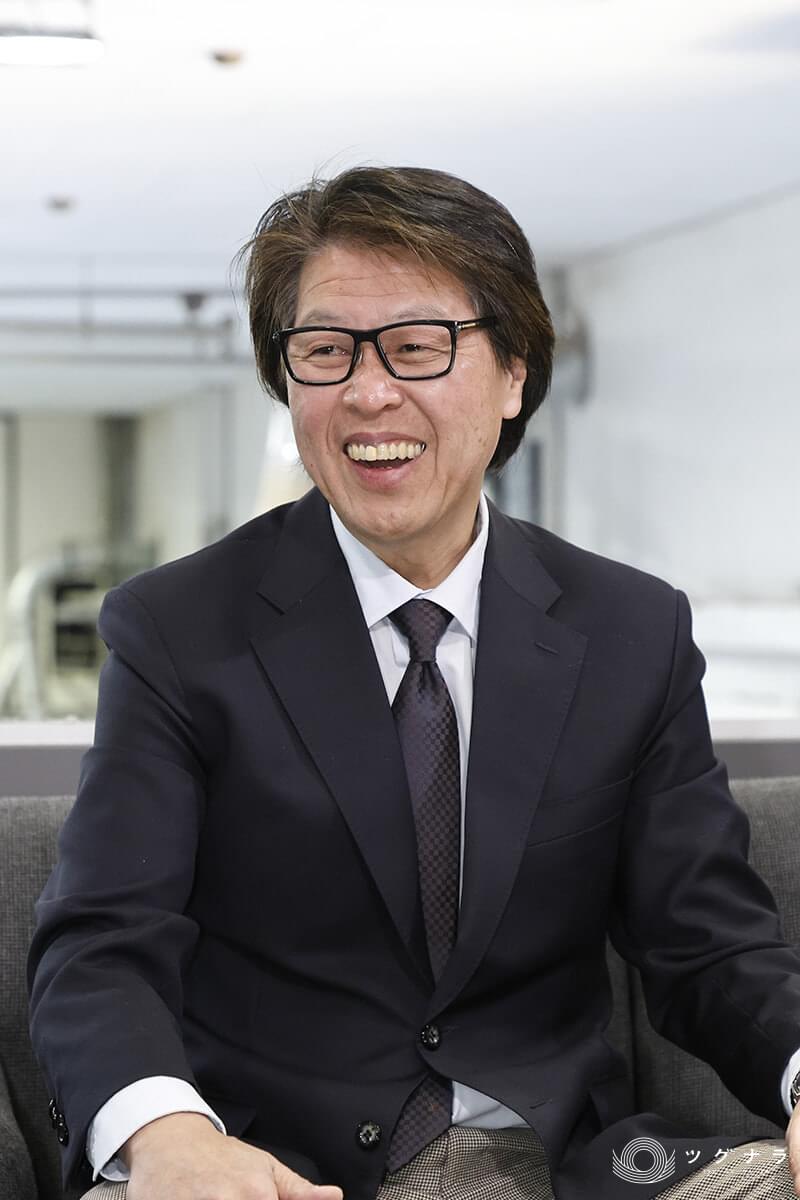
私たち豊桑産業株式会社は、1938年の創業以来、80年以上にわたり木工製品の製造を手掛けてきました。祖父の代から続くこの企業を4代目として引き継いだ私は、家業を継いだ当初から幾度も経営の危機に直面しましたが、その度に新しい挑戦を続けることで、危機を乗り越え、成長を遂げてきました。
私たちのスローガンは「一歩先ゆく木工会社」です。この言葉のもと、私たちは常に木工の可能性を信じ、より良い製品を提供し続けることを使命としています。特に、デジタル化の推進に力を入れており、独自の受注管理システムの開発や、製造プロセスのデジタル化を通じて、効率的で高品質な製品を提供できる体制を整えています。これにより、木工業界のモデルケースとして、地域の他企業からも注目されています。
また、2009年にはベトナムに現地法人を設立し、国際市場での競争力を高めるための一歩を踏み出しました。現地での生産拠点の確立により、コスト削減を実現し、新たなマーケットへの進出も果たしました。私たちは、これからも現状に満足することなく、さらに新しい技術やビジネスモデルを取り入れ、持続可能な成長を目指してまいります。
私たちがこれまで成し遂げてきた成功は、お客様のご要望や時代の変化に柔軟に対応し、常に最善を尽くしてきた結果です。今後も豊桑産業は、木工業界の発展に貢献し、さらなる発展を目指していきます。
代表取締役 織田 龍次
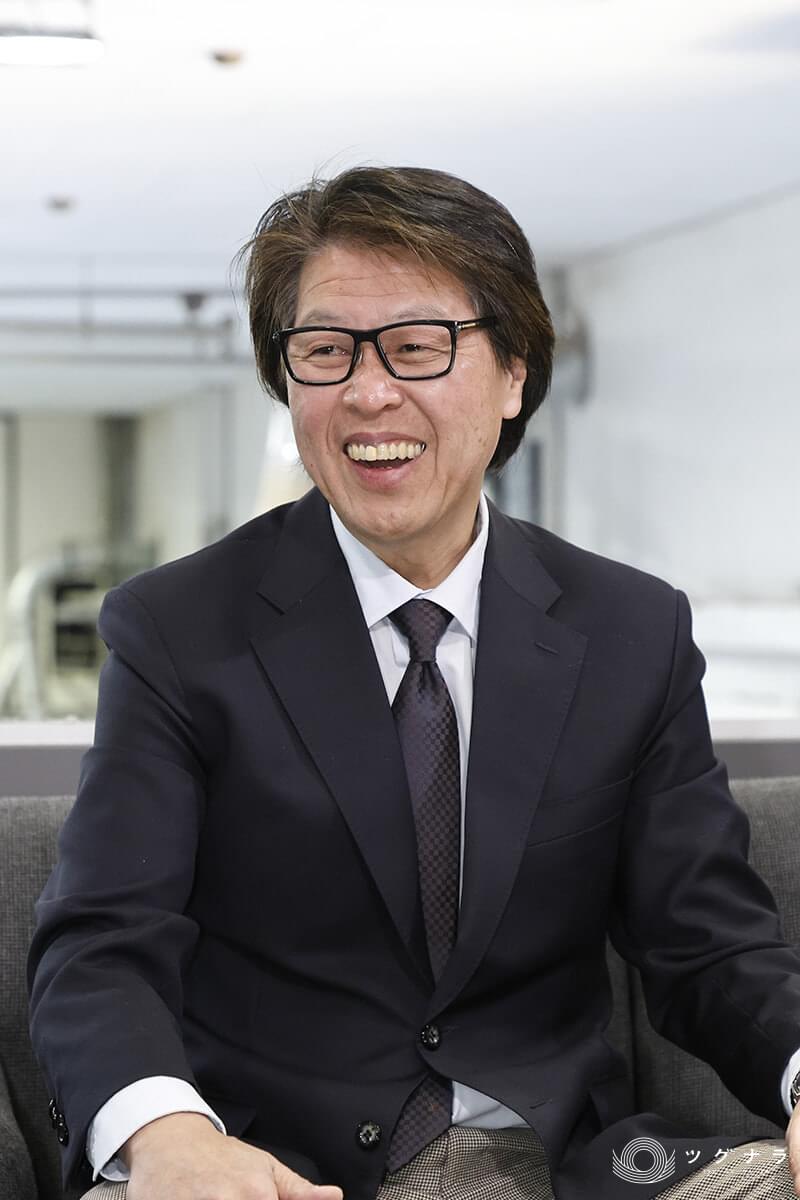
私たちのこだわり
初代は木製建具、2代目は人形ケース製造へと主事業を転換
豊桑産業株式会社は、祖父が1938年に愛知県丹羽郡扶桑町で創業した、織田木工所がルーツとなっています。創業当初は、木製の建具や家具の製造を主な事業としており、1960年には、五月人形や正月の羽子板飾りなどを収納する人形ケースの製造をスタートしました。当時は、戦後の高度経済成長によって日本全体が豊かになり、ベビーブームによって雛人形や五月人形のニーズが高まっており、祖父は需要のある仕事に携わることで安定化を図ろうとしたのかもしれません。
そして、人形ケース製造に事業を拡大した4年後に祖父は亡くなり、祖父の弟が2代目として家業を継ぐとともに、会社を法人化しました。
3代目の父の代には、木製の建具からアルミサッシ製造への転換を図りました。1960年代は、一般住宅の窓枠が木製からアルミサッシに置きかわった時期であり、先代は、人形ケース製造とともにニーズのある事業で新たな柱をつくろうとしたのだろうと思います。ところが、アルミサッシ製造は想定よりも伸びず、人形ケースの製造に注力するようになりました。しかし、人形ケースづくりは繁忙期と閑散期の振れ幅が大きく、収入は常に不安定であったため、経営も苦しい状況でした。
弟とともに塗装部門の内製化に踏み切る
私の学生時代には社内の人手不足も深刻で、私が進路選択の相談で就職の話をすると、当たり前のように家業を継ぐように言われ、私は大学を卒業してすぐ22歳で家業に入りました。
当時は人形ケースの製造が主事業でしたが、受注の波と経営の安定化が最大の課題でした。また、人形ケースの塗装は外部の協力工場にお願いしていましたが、なかなか納期を守ってもらえず、発注元との板挟みとなって大変な思いをしていました。私は商売の経験がなかったため自信がなく、言われるがままに仕事をしていましたが、このままでいいのかという疑問は常にもち続けていました。
そこで、後から大学を卒業し入社した弟とともに塗装部門の立ち上げを決断し、1989年に岐阜県各務原市で40坪ほどの小さな倉庫を借りて、自社の塗装を請け負うようになりました。塗装工程の内製化ができたことでコスト削減になり、納期や品質管理が強化されるようになりました。
さらに25歳の頃には、自社の人形ケースの塗装に加えて新規獲得に向けた営業も行ったことで、徐々に他の製品の受注も増え、閑散期の売り上げをカバーできるようになっていきました。体制や環境を常に改善していこうという姿勢は、塗装部門を設立したこの頃から続いていると感じています。
加工部門の立ち上げと内製化により創業時の建材・木工業へと立ち返る
繁忙期と閑散期の落差をカバーできるまでにはなりましたが、赤字続きだった経営を立て直すには決め手に欠ける状態が続いていました。そこに、大手建材メーカーのお客様から建材塗装の依頼があり、これを機に初代の祖父が立ち上げた木工業に、領域拡大という形で立ち返ることにしました。
しかし、当時の私は塗装をメインとしていたため加工までは手が回らず、外部の工場に加工をお願いしましたが、納期の問題で再び苦しい思いをすることとなってしまいました。大手との取引で信頼を獲得していくには、納期を守れる体制づくりが必要であり、塗装に加えて加工領域も内製化しようと決意しました。
当時はまだ人形ケースが主事業であり、経営は赤字の状態だったため先代には猛反対されましたが、経営の立て直しには必要な投資だと言い切り、加工部門の立ち上げのために約1000万円を投資して、コンピュータ制御で切削加工ができるNC加工機を導入しました。軌道に乗せるまでは大変でしたが、協力工場に依存せず自社での一貫生産体制を確立したことで、納期短縮とコスト削減につなげることができました。
2度の火事と取引先の事業移管による経営の危機
100坪の工場に加工機を2台置き、加工と塗装を行うようになった頃、人形ケースをつくっていた本社工場の方で火災が起こりました。作業場が半焼し、先代が火事で怪我を負ったため、急遽私が代表に就任することとなりました。経営者となり事後処理や対応に追われていましたが、次の年に再び火災が起こり、加工や塗装を行っていた100坪の工場も大きな被害を受けました。
そのような中で、大手建材業から突然新たな仕事を依頼され、仕事をいただけるならありがたいと、弟と必死になって仕事をこなしました。しかしその仕事は、取引先が事業移管をする間の限定的な仕事であると後から知らされ、担当の方からは「このままでは仕事がなくなってしまう、何でもいいから提案しなさい」と言われました。当時は、その取引先が弊社の売上のほぼ100%を占めている状態であり、災難続きで窮地に追い込まれたような状況でした。
数カ月間悩み、担当の方が再び訪れた時には、弊社が最も得意とする「エッジ塗装カウンター」を提案しました。エッジ塗装カウンターは、メラミン化粧板に耐水MDFを貼り、裏面と木口に塗装をかけた商品です。提案時は却下されましたが、数週間後には商品化が決まり、生産をスタートすることとなりました。
エッジ塗装カウンターは、生産開始から1年目はまずまずの売上でしたが、2年目にはFAXのロール感熱紙が朝晩止まらないほどの受注が寄せられるようになりました。一気に黒字にはなったものの、当時使っていたFAXは通信速度が遅く、受注はすべてエクセルで管理していたため、あっという間に受注管理が追いつかなくなりました。どの商品をつくるのか、出荷したかどうかまでわからなくなり、取引先を巻き込んで大クレームへと発展しました。緊急対応として、取引先の社員が毎日10人ほど事務所につめ、壁全面に発注書を貼り、出荷したものから順番にはがしていく仕組みで難を乗り切りましたが、受注管理の破綻という苦い経験を契機に、デジタル化への投資を真剣に考えるようになりました。
「インダストリー4.0」のモデルとDXで切り拓く新たな競争力
木工業の歴史は古く、現在も手作業で加工を行っている同業は多くあります。弊社としては安定的な商品提供と生産性向上が念頭にあり、木工業界に先駆けて独自の受注管理システムの開発や、製造プロセスのデジタル化を進めようと決めました。
デジタル化への挑戦を決めたきっかけとなったのは、単品の特注品を製造しているドイツの工場を見学した時でした。ドイツは世界有数の木材消費国であり、林業や木材加工が盛んです。ドイツ政府は、木材加工を含む製造業の生産プロセスの効率化として「インダストリー4.0」を推進しており、IoTやクラウドコンピューティングの活用により、柔軟で持続可能な生産の実現を目指しています。木工加工は木くずなどが散らばりやすいのですが、私が見学した木工加工場はクリーンで、設備やシステムが充実していました。「ここまで立派にはできなくとも、自社でシステムを構築したい」と思い、ドイツの工場を参考にデジタル化を進めることにしました。
弊社では「基幹システム」と呼ぶ自社の生産管理システムを構築し、さらにドイツのHOMAG社のソフトと設備を導入して、一括管理のためにお客様先のソフトと設備の紐づけ作業を行いました。HOMAG社の設備やソフトは、プログラムが共通化されているので汎用性があり、自社のあらゆる種類の機械や加工機も同じルールで動かすことができます。弊社では、HOMAGソフトの汎用性をフル活用した独自システムを構築し、受注出荷やトラブル発生時の対応まで、あらゆる情報をシステムに落とし込んでいくことで、ノウハウとして蓄積させていけるように整備しました。
OCR、AIなどのソフトとも複雑に絡み合った弊社独自のシステムは、他社には真似できないレベルにまでに育ってきています。お客様によってオーダーの仕方は図面一つをとってもアナログ、デジタルで違うため、受注したデータはすべて2016年に開設したベトナムのフエにあるCADセンターに送り、形式の統一と一括管理ができるようにしています。基幹システムの構築により、複数の工場が同じ場所にあるかのように連携して動くことができるようになり、全体の生産性が向上しました。
国内でも、ドイツの「インダストリー4.0」の考え方をベースにした「コネクテッド・インダストリーズ」という官民の政策が策定されていますが、施策が浸透し会社の業績や社会の利益としてあらわれるまでには、かなりの時間がかかると考えています。弊社が業界のモデルケースとして新しい技術を取り入れながら、生産効率や品質を向上させていくことで、同業や異業種の企業が前進するきっかけになれたらと思っています。ゆくゆくは、誰もが働きやすい「ユニバーサル・スマートファクトリー」を目指していきたい考えです。
デジタル化に反対していた社内を実践力でまとめあげる
社員は、現在は弊社のデジタル化への方針について理解してくれていますが、生産管理システムのデジタル移行時は、社内のほぼ全員が反対でした。どんなに「仕事が楽になる」と伝えても、社員としては「仕事を覚え直さなければいけない」という考えが先立ってしまうようであり、溝が埋まらない状態が続きました。しばらくは説得を続けていましたが、社員の意識や行動をいきなり変えることは難しいと考え、まずは社内のレイアウトを変え、設備やソフトを入れて仕事を用意することで、頭よりも先に手を動かしながら覚えていける環境をつくりました。
目の前に仕事があることで、社員も当たり前のように作業ができるようになり、さほど時間もかからず順応してくれました。営業も、仕事を獲得しようと努力し続けた結果が出始めており、現場との相乗効果が生まれつつあります。また、ベトナム現地の社員たちは、大学を出て日本語で仕事をしたいという意欲的な方が多く、日本語の手書きの発注書をデータ化する作業も、プライドを持ってこなしてくれています。
ここまで社員がついてきてくれているのは、実際に作業が楽になり、頑張った分だけ業績や賃上げという形で成果が返ってきているからだと思います。以前は私が電話に出て対応をしなければいけないことが多かったのですが、システム化されたことで全社員が工程や会社の状態を把握し、各部署で対応できるようになり、経営者の私自身も楽になりました。デジタル化の構想から足かけ10年で、ようやくここまでたどり着くことができたと、今実感しています。
企業のDNAとしての経営理念
豊桑産業のスローガンは「一歩先ゆく木工会社」です。このスローガンのもと、お客様、お取引先、従業員と共に、木工の可能性を信じて事業に取り組んでいます。また、私たちの経営理念である「常に夢と目標を持ち続け、新しい価値を創造し続けること」は、創業以来一貫して掲げてきたものであり、全社員がその精神を共有し、日々の業務に反映しています。
経営理念を実現するため、デジタル技術の活用を重視し、効率的な生産体制の構築や品質向上に向けた取り組みを続けています。こうしたDX化の取り組みを通じて、経営理念は単なるスローガンではなく、実際の行動指針として社員の心に深く根付いています。
豊桑産業が80年以上の歴史を刻むことができたのは、お客様のご要望や時代の変化を柔軟に受け入れ、最善を尽くしてきた結果であると考えています。私たちは、現状に満足することなく、お客様の事業と社会に貢献しながら、持続的な成長を目指していきたいです。
地域企業のモデルとして工場見学と取引先のシステム化を支援
弊社のデジタル化の取り組みは、地域や他県の企業からも高く評価され、システムを学びたいという方々のために工場を公開しています。工場見学の時には、デジタル化やIoTについて相談を受けることもありますが、どの企業も課題が多く、国内の製造業全体のデジタル化の難しさを実感しています。弊社に視察に訪れた航空産業企業の方は、非常に高度な技術を持ちながらも、部分的にしかデジタル化が進んでいない自社の現状に悩みを抱えており、製造プロセス全体を共通化し一元管理するシステムの導入はハードルが高いと話していました。
企業の規模が大きいほど、既存のシステムからの転換は難しいため、弊社では自社の周囲から少しずつでもデジタル化を進めていこうと考え、関連する取引先の支援を行うようになりました。弊社の協力工場の場合は、システム化が進んでいないことで弊社の倍のコストがかかっていることがわかり、現在はコストダウンに向けた技術協力という形で、弊社がソフト面での支援を行っています。ハード面の整備は協力工場側で受け持ってもらい、バーコードスキャンのシステム導入支援を進めているところです。
システムが構築されれば、その仕事に携わる社員は最小限で済むようになりますが、省人化として社員を辞めさせるのではなく、生産力のキャパシティが増えると捉えて、新しい仕事を確保して雇用を続ける努力をしてほしいとお話しするようにしています。協力会社への支援のように、デジタル技術を活用し、互いに強みを補完し合いながら、共に成長していくためのパートナーシップを築き上げていくことで、より多くの企業が利益を上げられる環境を整えたいと考えています。
事業体の垣根を超え、木工業存続のため協力し合える仕組みづくりを目指す
木工業界は、設備はあっても後継者がいなかったり、DXの流れについていけず諦めてしまったりしている経営者さんが多く、非常に勿体ないと感じています。裏を返せば、問題を抱えている企業さんと弊社が連携することで、格段にいい方向へと進んで行ける可能性を秘めているのです。
国内の木工業は、林業の衰退や輸入木材の不足による高騰などで今後さらに厳しくなる見通しであり、自社への思いをもちつつ、会社やグループという事業体の垣根を越えて協力し合える「インダストリー4.0」のような仕組みづくりがますます必要になると見ています。
今後さらに円安が進めば、ベトナムで製造した製品の方が高くなりますが、海外でも関連企業を中心に協力し合える体制をつくり上げることができれば、外部環境の変化も乗り切れるはずです。
機械やシステムを使いきれていない同業の方も、弊社に協力していただくことで確実に稼働率や生産性を上げることができます。弊社の経験や仕組みを活かし、資本関係のしがらみなくグローバル市場での競争力を高めながら生産力を向上させ、木工業が今後も続いていけるような基盤を築き上げることが私の理想です。
未来を見据えたホールディングス化により持続可能な成長への道を探る
近い将来は、弊社が運営するベトナムの現地法人と株式会社HOAO(障害者就労継続支援事業所)をホールディングス化することで、M&Aや他社とのパートナーシップや共同プロジェクトの選択肢を広げていきたい考えです。また、私自身が今年60歳になるので、いつまで働くかを決めて、後継者にスムーズに事業を引き継ぐための準備も並行して進めていきたいと考えています。
今後はさらに多くの企業と連携し、デジタル技術を活用した新しい価値創造に取り組んでいくことも重要になってくると思います。木工業界において、デジタル化はまだまだ発展途上にありますが、私たちはこの分野でのモデルケースとしてリーダーシップを発揮し、業界全体の成長に貢献していきたいです。
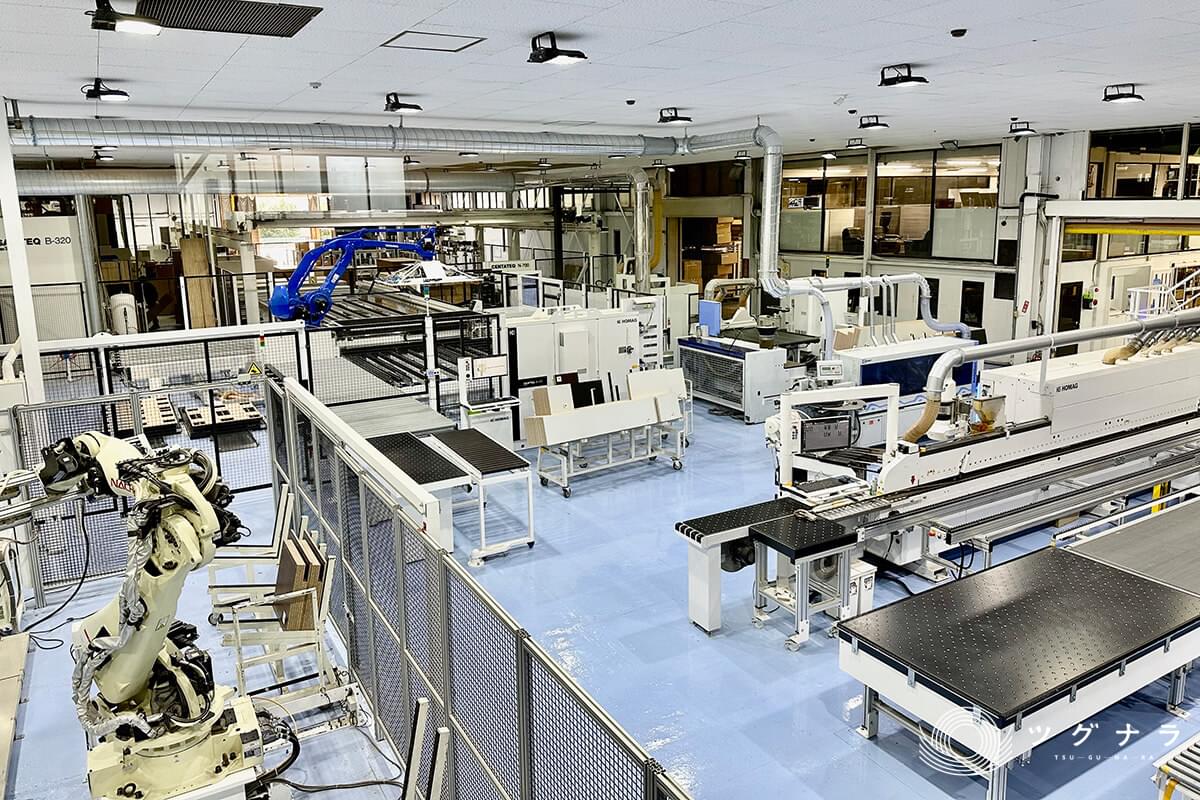
初代は木製建具、2代目は人形ケース製造へと主事業を転換
豊桑産業株式会社は、祖父が1938年に愛知県丹羽郡扶桑町で創業した、織田木工所がルーツとなっています。創業当初は、木製の建具や家具の製造を主な事業としており、1960年には、五月人形や正月の羽子板飾りなどを収納する人形ケースの製造をスタートしました。当時は、戦後の高度経済成長によって日本全体が豊かになり、ベビーブームによって雛人形や五月人形のニーズが高まっており、祖父は需要のある仕事に携わることで安定化を図ろうとしたのかもしれません。
そして、人形ケース製造に事業を拡大した4年後に祖父は亡くなり、祖父の弟が2代目として家業を継ぐとともに、会社を法人化しました。
3代目の父の代には、木製の建具からアルミサッシ製造への転換を図りました。1960年代は、一般住宅の窓枠が木製からアルミサッシに置きかわった時期であり、先代は、人形ケース製造とともにニーズのある事業で新たな柱をつくろうとしたのだろうと思います。ところが、アルミサッシ製造は想定よりも伸びず、人形ケースの製造に注力するようになりました。しかし、人形ケースづくりは繁忙期と閑散期の振れ幅が大きく、収入は常に不安定であったため、経営も苦しい状況でした。
弟とともに塗装部門の内製化に踏み切る
私の学生時代には社内の人手不足も深刻で、私が進路選択の相談で就職の話をすると、当たり前のように家業を継ぐように言われ、私は大学を卒業してすぐ22歳で家業に入りました。
当時は人形ケースの製造が主事業でしたが、受注の波と経営の安定化が最大の課題でした。また、人形ケースの塗装は外部の協力工場にお願いしていましたが、なかなか納期を守ってもらえず、発注元との板挟みとなって大変な思いをしていました。私は商売の経験がなかったため自信がなく、言われるがままに仕事をしていましたが、このままでいいのかという疑問は常にもち続けていました。
そこで、後から大学を卒業し入社した弟とともに塗装部門の立ち上げを決断し、1989年に岐阜県各務原市で40坪ほどの小さな倉庫を借りて、自社の塗装を請け負うようになりました。塗装工程の内製化ができたことでコスト削減になり、納期や品質管理が強化されるようになりました。
さらに25歳の頃には、自社の人形ケースの塗装に加えて新規獲得に向けた営業も行ったことで、徐々に他の製品の受注も増え、閑散期の売り上げをカバーできるようになっていきました。体制や環境を常に改善していこうという姿勢は、塗装部門を設立したこの頃から続いていると感じています。
加工部門の立ち上げと内製化により創業時の建材・木工業へと立ち返る
繁忙期と閑散期の落差をカバーできるまでにはなりましたが、赤字続きだった経営を立て直すには決め手に欠ける状態が続いていました。そこに、大手建材メーカーのお客様から建材塗装の依頼があり、これを機に初代の祖父が立ち上げた木工業に、領域拡大という形で立ち返ることにしました。
しかし、当時の私は塗装をメインとしていたため加工までは手が回らず、外部の工場に加工をお願いしましたが、納期の問題で再び苦しい思いをすることとなってしまいました。大手との取引で信頼を獲得していくには、納期を守れる体制づくりが必要であり、塗装に加えて加工領域も内製化しようと決意しました。
当時はまだ人形ケースが主事業であり、経営は赤字の状態だったため先代には猛反対されましたが、経営の立て直しには必要な投資だと言い切り、加工部門の立ち上げのために約1000万円を投資して、コンピュータ制御で切削加工ができるNC加工機を導入しました。軌道に乗せるまでは大変でしたが、協力工場に依存せず自社での一貫生産体制を確立したことで、納期短縮とコスト削減につなげることができました。
2度の火事と取引先の事業移管による経営の危機
100坪の工場に加工機を2台置き、加工と塗装を行うようになった頃、人形ケースをつくっていた本社工場の方で火災が起こりました。作業場が半焼し、先代が火事で怪我を負ったため、急遽私が代表に就任することとなりました。経営者となり事後処理や対応に追われていましたが、次の年に再び火災が起こり、加工や塗装を行っていた100坪の工場も大きな被害を受けました。
そのような中で、大手建材業から突然新たな仕事を依頼され、仕事をいただけるならありがたいと、弟と必死になって仕事をこなしました。しかしその仕事は、取引先が事業移管をする間の限定的な仕事であると後から知らされ、担当の方からは「このままでは仕事がなくなってしまう、何でもいいから提案しなさい」と言われました。当時は、その取引先が弊社の売上のほぼ100%を占めている状態であり、災難続きで窮地に追い込まれたような状況でした。
数カ月間悩み、担当の方が再び訪れた時には、弊社が最も得意とする「エッジ塗装カウンター」を提案しました。エッジ塗装カウンターは、メラミン化粧板に耐水MDFを貼り、裏面と木口に塗装をかけた商品です。提案時は却下されましたが、数週間後には商品化が決まり、生産をスタートすることとなりました。
エッジ塗装カウンターは、生産開始から1年目はまずまずの売上でしたが、2年目にはFAXのロール感熱紙が朝晩止まらないほどの受注が寄せられるようになりました。一気に黒字にはなったものの、当時使っていたFAXは通信速度が遅く、受注はすべてエクセルで管理していたため、あっという間に受注管理が追いつかなくなりました。どの商品をつくるのか、出荷したかどうかまでわからなくなり、取引先を巻き込んで大クレームへと発展しました。緊急対応として、取引先の社員が毎日10人ほど事務所につめ、壁全面に発注書を貼り、出荷したものから順番にはがしていく仕組みで難を乗り切りましたが、受注管理の破綻という苦い経験を契機に、デジタル化への投資を真剣に考えるようになりました。
「インダストリー4.0」のモデルとDXで切り拓く新たな競争力
木工業の歴史は古く、現在も手作業で加工を行っている同業は多くあります。弊社としては安定的な商品提供と生産性向上が念頭にあり、木工業界に先駆けて独自の受注管理システムの開発や、製造プロセスのデジタル化を進めようと決めました。
デジタル化への挑戦を決めたきっかけとなったのは、単品の特注品を製造しているドイツの工場を見学した時でした。ドイツは世界有数の木材消費国であり、林業や木材加工が盛んです。ドイツ政府は、木材加工を含む製造業の生産プロセスの効率化として「インダストリー4.0」を推進しており、IoTやクラウドコンピューティングの活用により、柔軟で持続可能な生産の実現を目指しています。木工加工は木くずなどが散らばりやすいのですが、私が見学した木工加工場はクリーンで、設備やシステムが充実していました。「ここまで立派にはできなくとも、自社でシステムを構築したい」と思い、ドイツの工場を参考にデジタル化を進めることにしました。
弊社では「基幹システム」と呼ぶ自社の生産管理システムを構築し、さらにドイツのHOMAG社のソフトと設備を導入して、一括管理のためにお客様先のソフトと設備の紐づけ作業を行いました。HOMAG社の設備やソフトは、プログラムが共通化されているので汎用性があり、自社のあらゆる種類の機械や加工機も同じルールで動かすことができます。弊社では、HOMAGソフトの汎用性をフル活用した独自システムを構築し、受注出荷やトラブル発生時の対応まで、あらゆる情報をシステムに落とし込んでいくことで、ノウハウとして蓄積させていけるように整備しました。
OCR、AIなどのソフトとも複雑に絡み合った弊社独自のシステムは、他社には真似できないレベルにまでに育ってきています。お客様によってオーダーの仕方は図面一つをとってもアナログ、デジタルで違うため、受注したデータはすべて2016年に開設したベトナムのフエにあるCADセンターに送り、形式の統一と一括管理ができるようにしています。基幹システムの構築により、複数の工場が同じ場所にあるかのように連携して動くことができるようになり、全体の生産性が向上しました。
国内でも、ドイツの「インダストリー4.0」の考え方をベースにした「コネクテッド・インダストリーズ」という官民の政策が策定されていますが、施策が浸透し会社の業績や社会の利益としてあらわれるまでには、かなりの時間がかかると考えています。弊社が業界のモデルケースとして新しい技術を取り入れながら、生産効率や品質を向上させていくことで、同業や異業種の企業が前進するきっかけになれたらと思っています。ゆくゆくは、誰もが働きやすい「ユニバーサル・スマートファクトリー」を目指していきたい考えです。
デジタル化に反対していた社内を実践力でまとめあげる
社員は、現在は弊社のデジタル化への方針について理解してくれていますが、生産管理システムのデジタル移行時は、社内のほぼ全員が反対でした。どんなに「仕事が楽になる」と伝えても、社員としては「仕事を覚え直さなければいけない」という考えが先立ってしまうようであり、溝が埋まらない状態が続きました。しばらくは説得を続けていましたが、社員の意識や行動をいきなり変えることは難しいと考え、まずは社内のレイアウトを変え、設備やソフトを入れて仕事を用意することで、頭よりも先に手を動かしながら覚えていける環境をつくりました。
目の前に仕事があることで、社員も当たり前のように作業ができるようになり、さほど時間もかからず順応してくれました。営業も、仕事を獲得しようと努力し続けた結果が出始めており、現場との相乗効果が生まれつつあります。また、ベトナム現地の社員たちは、大学を出て日本語で仕事をしたいという意欲的な方が多く、日本語の手書きの発注書をデータ化する作業も、プライドを持ってこなしてくれています。
ここまで社員がついてきてくれているのは、実際に作業が楽になり、頑張った分だけ業績や賃上げという形で成果が返ってきているからだと思います。以前は私が電話に出て対応をしなければいけないことが多かったのですが、システム化されたことで全社員が工程や会社の状態を把握し、各部署で対応できるようになり、経営者の私自身も楽になりました。デジタル化の構想から足かけ10年で、ようやくここまでたどり着くことができたと、今実感しています。
企業のDNAとしての経営理念
豊桑産業のスローガンは「一歩先ゆく木工会社」です。このスローガンのもと、お客様、お取引先、従業員と共に、木工の可能性を信じて事業に取り組んでいます。また、私たちの経営理念である「常に夢と目標を持ち続け、新しい価値を創造し続けること」は、創業以来一貫して掲げてきたものであり、全社員がその精神を共有し、日々の業務に反映しています。
経営理念を実現するため、デジタル技術の活用を重視し、効率的な生産体制の構築や品質向上に向けた取り組みを続けています。こうしたDX化の取り組みを通じて、経営理念は単なるスローガンではなく、実際の行動指針として社員の心に深く根付いています。
豊桑産業が80年以上の歴史を刻むことができたのは、お客様のご要望や時代の変化を柔軟に受け入れ、最善を尽くしてきた結果であると考えています。私たちは、現状に満足することなく、お客様の事業と社会に貢献しながら、持続的な成長を目指していきたいです。
地域企業のモデルとして工場見学と取引先のシステム化を支援
弊社のデジタル化の取り組みは、地域や他県の企業からも高く評価され、システムを学びたいという方々のために工場を公開しています。工場見学の時には、デジタル化やIoTについて相談を受けることもありますが、どの企業も課題が多く、国内の製造業全体のデジタル化の難しさを実感しています。弊社に視察に訪れた航空産業企業の方は、非常に高度な技術を持ちながらも、部分的にしかデジタル化が進んでいない自社の現状に悩みを抱えており、製造プロセス全体を共通化し一元管理するシステムの導入はハードルが高いと話していました。
企業の規模が大きいほど、既存のシステムからの転換は難しいため、弊社では自社の周囲から少しずつでもデジタル化を進めていこうと考え、関連する取引先の支援を行うようになりました。弊社の協力工場の場合は、システム化が進んでいないことで弊社の倍のコストがかかっていることがわかり、現在はコストダウンに向けた技術協力という形で、弊社がソフト面での支援を行っています。ハード面の整備は協力工場側で受け持ってもらい、バーコードスキャンのシステム導入支援を進めているところです。
システムが構築されれば、その仕事に携わる社員は最小限で済むようになりますが、省人化として社員を辞めさせるのではなく、生産力のキャパシティが増えると捉えて、新しい仕事を確保して雇用を続ける努力をしてほしいとお話しするようにしています。協力会社への支援のように、デジタル技術を活用し、互いに強みを補完し合いながら、共に成長していくためのパートナーシップを築き上げていくことで、より多くの企業が利益を上げられる環境を整えたいと考えています。
事業体の垣根を超え、木工業存続のため協力し合える仕組みづくりを目指す
木工業界は、設備はあっても後継者がいなかったり、DXの流れについていけず諦めてしまったりしている経営者さんが多く、非常に勿体ないと感じています。裏を返せば、問題を抱えている企業さんと弊社が連携することで、格段にいい方向へと進んで行ける可能性を秘めているのです。
国内の木工業は、林業の衰退や輸入木材の不足による高騰などで今後さらに厳しくなる見通しであり、自社への思いをもちつつ、会社やグループという事業体の垣根を越えて協力し合える「インダストリー4.0」のような仕組みづくりがますます必要になると見ています。
今後さらに円安が進めば、ベトナムで製造した製品の方が高くなりますが、海外でも関連企業を中心に協力し合える体制をつくり上げることができれば、外部環境の変化も乗り切れるはずです。
機械やシステムを使いきれていない同業の方も、弊社に協力していただくことで確実に稼働率や生産性を上げることができます。弊社の経験や仕組みを活かし、資本関係のしがらみなくグローバル市場での競争力を高めながら生産力を向上させ、木工業が今後も続いていけるような基盤を築き上げることが私の理想です。
未来を見据えたホールディングス化により持続可能な成長への道を探る
近い将来は、弊社が運営するベトナムの現地法人と株式会社HOAO(障害者就労継続支援事業所)をホールディングス化することで、M&Aや他社とのパートナーシップや共同プロジェクトの選択肢を広げていきたい考えです。また、私自身が今年60歳になるので、いつまで働くかを決めて、後継者にスムーズに事業を引き継ぐための準備も並行して進めていきたいと考えています。
今後はさらに多くの企業と連携し、デジタル技術を活用した新しい価値創造に取り組んでいくことも重要になってくると思います。木工業界において、デジタル化はまだまだ発展途上にありますが、私たちはこの分野でのモデルケースとしてリーダーシップを発揮し、業界全体の成長に貢献していきたいです。
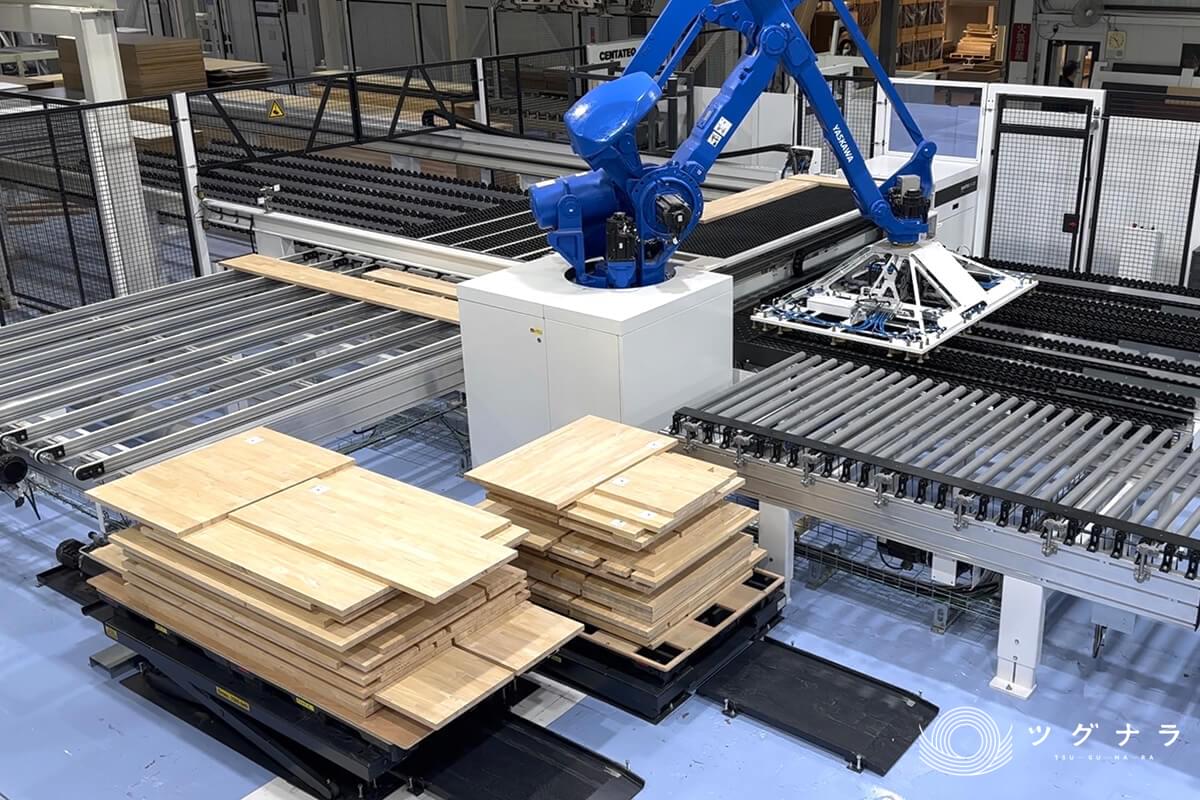
会社概要
社名 | 豊桑産業株式会社 |
創立年 | 1938年 |
代表者名 | 代表取締役 織田 龍次 |
資本金 | 3000万円 |
事業エリア |
扶桑工場(本店所在地)
480-0102 愛知県丹羽郡扶桑町高雄字天道434 |
ベトナム フエ支店(CADセンター)
7th Floor, No. 28 Ly Thuong Kiet Street, Vinh Ninh Ward, Hue City, Thua Thien Hue Province, VietNam. |
|
ベトナム ダナン工場
Lot B1, Road No.3, Hoa Khanh Industrial zone, Lien Chieu Dist., Danang, Vietnam, |
|
本社住所 |
509-0146 岐阜県各務原市鵜沼三ツ池町6丁目424番地1 |
事業内容 | 木製家具製造業(カウンター・キャビネット・造作材など) |
URL |
https://hosojapan.co.jp/
|
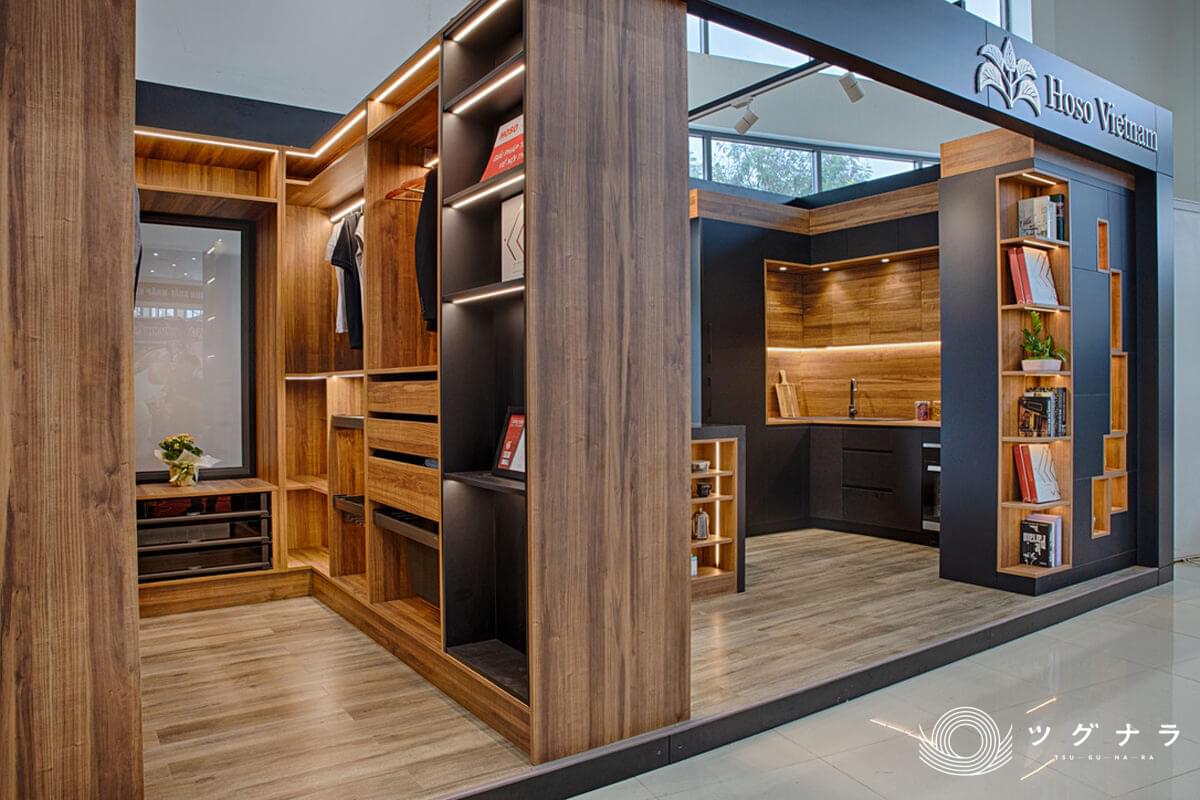
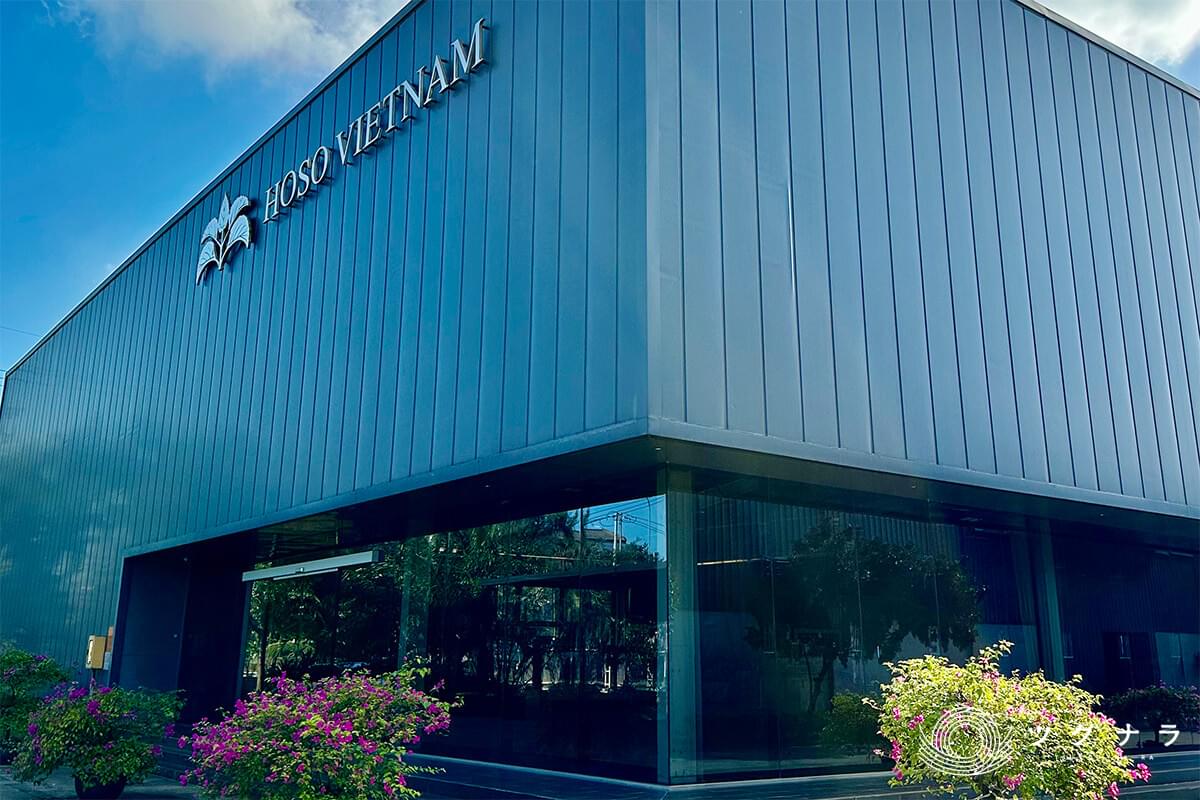
会社沿革
1938年 | 織田木工所開設 建具事業開始 |
1960年 | 人形ケース製造事業開始 |
1964年 | 法人設立 アルミサッシ製造事業開始 |
1989年 | 塗装部開設 |
1995年 | 建材製造事業開始 |
1997年 | 岐阜県各務原市朝日町に第2工場設 |
2004年 | 岐阜県各務原市三ツ池町に各務原工場設置 |
2007年 | 各務原工場土地取得 |
2008年 | 朝日工場開設 |
2009年 | ベトナムでHoso Vietnam Co.,ltdを設立(2009年10月より工場稼動) ISO9001 認証取得 |
2010年 | 有限会社から株式会社に組織変更 |
2011年 | Hoso Vietnam増資 |
2012年 | 朝日工場、三ツ池工場を集約し新工場へ移転 Hoso Vietnam工場完成・移転 |
2014年 | 障がい者就労支援施設(株式会社HOAO)の設置 |
2016年 | 自動塗装機の導入 Hoso Vietnam Hue支所開所 アナログからデジタル化するためのCADセンター開設 |
2018年 | 製造プロセスのデジタル化 スマートファクトリー化 |
2021年 | 資本金を3000万円に増資 Hoso Vietnam キャビネット新工場完成 生産開始 |
2022年 | カーボンニュートラルへの取り組み「SBTイニシアチブ(Science Based Targets initiative)」の認証を取得 ISO14001 認証取得 |
2024年 | 健康経営優良法人に認定 |
豊桑産業株式会社の経営資源引継ぎ募集情報
公開日:2024/11/13 (2024/12/19修正)
※本記事の内容および所属名称は2024年12月現在のものです。現在の情報とは異なる場合があります。